Benefit from Leader Standard Work
American Lean Weekday: Leadership | Lean Culture & Intrapreneurship | Lean Methods | Industry 4.0 | Case Studies - A podcast by Tom Reed: Lean Enthusiast & President of American Lean
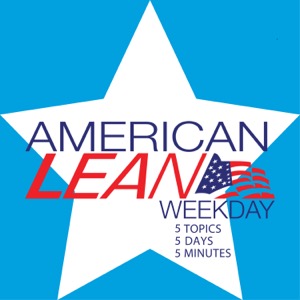
Categories:
Two weeks ago, I introduced the concept of a layered approach to support your sustain efforts. This week I want to go into more depth on Leader Standard Work.First, let’s do a re-cap. The three layers of support are coaching cards, leader standard work, and management or Gemba walks. Each layer supports the layer above it.Operator Coaching CardsThese are elements of standard work that we want the team members to complete each day within their work area. This is a great way to sustain your 6S. You can put the elements you want to be completed each day on a coaching card.Management (Gemba) WalksGemba means to go to where the value is added. This is the top-level in the three levels of sustain.I coach companies to conduct their management walks one a month with the leadership team. This gets everyone out of the offices and to the shop floor to “see” what is happening.Leader Standard Work (LSW)Those are the first and third levels of sustain. Leader Standard Work, often abbreviated LSW is just like it sounds. These are activities that the supervisor or area lead should complete each day.Depending upon what roles you have in the business, your LSW can take up more of your day, or very little of your day.Since most managers, directors, and executives aren’t guided by more than a job description, there isn’t much in the way of daily structure. They should use Leader Standard Work although it may take only a few minutes a day.They should check on the business KPI’s. They should follow the numbers for their area or business unit. They should check on the status of strategic initiatives they are driving. If proper communication dashboards are developed this may consume little of their day.A large piece of their day should comprise daily mentoring and coaching of their direct reports. Changing a culture across an organization takes a lot of mentoring and coaching. Not only are there Lean methods to incorporate, but a servant leadership mindset also needs to be allowed to form and take root.For a supervisor, coaching cards are more process-driven. Take a walk through the area five times a day. Hold a daily stand-up meeting. Watch the shift start-up process.Prepare tomorrow’s labor plan. Measure hourly production. Monitor and observe the coaching card completion. Monitor in-process Kanban discipline. These are all activities that a supervisor can monitor daily.Check with your leadership mentor and reflect on what is going well and not well. Discuss struggles and work together to develop solutions. Discuss how the adoption of the Lean Management System is coming along.If you deploy LSW within your organization, you will be amazed at how quickly your business will improve.As always it is an honor to serve you and I hope that you and your company are getting better every day!Rate and Review HereMore show notes are hereSchedule a free 1/2 call with Tom Reed.Buy the Lean Game PlanFollow me on