Replay- Did You Know there is an Industry 5.0?
American Lean Weekday: Leadership | Lean Culture & Intrapreneurship | Lean Methods | Industry 4.0 | Case Studies - A podcast by Tom Reed: Lean Enthusiast & President of American Lean
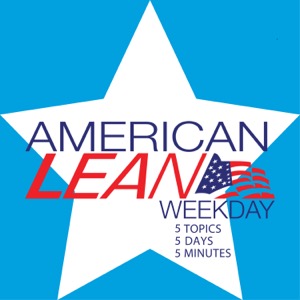
Categories:
It seems like we are just learning about Industry 4.0 and the enablers that will impact that digital transformation. Now companies are discussing what Industry 5.0 looks like.Earlier in the year, I talked about the use of cobots to support Industry 4.0. Industry 5.0 is based on humans and robots working together in close proximity. Given the advances in sensors, cobots no longer need to be kept in a cage away from humans.Smart sensors deployed on a cobot allow the cobot to work directly on an assembly line alongside human counterparts. Some of the smaller cobots only weigh 30 pounds and can handle about 6 pounds of material. These cobots can complete tasks such as screwing screws or tightening bolts into place. Tasks typically completed by humans today.Larger cobots can handle activities like machine tending, packaging, material handling and driving larger screws and tightening bolts. Given a large variety of grippers, they can handle many tasks.How will this drive Industry 5.0?1. They will be deployed to improve the customization of mass-produced productsImagine if Sony 3D printed the outer case of a PS5. Yes, the new Playstation due at any time from Sony. What if you were giving this as a Holiday gift and wanted to engrave a personal note on the outer case. A Cobot could handle engraving unit after unit with each note being unique.No setup required. Customer units could be kicked off the production line and a cobot could add the customization and the unit could be added back to the production line to continue its journey into a box.2. Product InspectionCobots can be used as the primary inspection tool for products and suspect units can be routed to an employee for further verification. They could be deployed alongside employees in a line and using vision sensors ensure that the employee completed the work required at their operation.Product assembly errors are dramatically reduced when a cobot is part of a check, do, check scenario.3. Deburring and CNC machine tendingWhat would happen in your machine shop if a cobot could unload machined parts from a CNC machine, deburr the parts and then neatly stack them for movement to the next machining operation?Advances in deburring flat and rough surfaces are happening at a rapid pace. Having a cobot arm next to the machinist would allow the machinist to monitor and manage additional machines.Reducing deburr operations means there is less “blending” of a surface that a talented deburr operator needs to accomplish. They can focus on completing more complicated deburr work that the cobot can’t complete.In Industry 5.0 your co-worker might not want to go out after work for beers, but it will help you get more done and make your work a whole lot easier!As always it is an honor to serve you and I hope that you and your company are getting better every day!Rate and Review HereMore show notes are hereSchedule a free 1/2 call with Tom Reed.Buy the Lean Game PlanFollow me on