Is Investing In Process Automation In The Factory Worth It? (+ Implementation Best Practices)
China Manufacturing Decoded - A podcast by Sofeast - Fridays
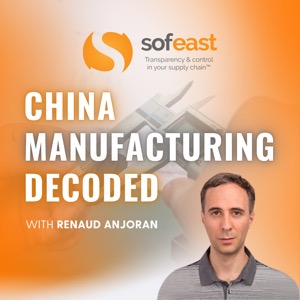
In This Episode... Adrian asks Renaud the questions: "Is Investing In Process Automation In The Factory Worth It?" and "What are the best practices to follow to smoothly transition into more automation?" In China especially, there's a trend to replace staff with equipment, and part of this automation drive comes from the government itself who is steering the manufacturing sector towards higher-tech products. As staff costs rise, the temptation to use equipment and robots due to the seemingly lower cumulative cost over time is understandable, but is process automation truly worth it, and If we do want to implement automation into the factory, what are the best practices to follow to make it a smooth transition? That's what we get into here... Show Notes 00:00 - Introducing the episode 02:35 - Summarising process automation in the factory - essentially it's the use of equipment and software to replace human labor. This sounds great and can be, but this episode aims to dispel a lot of the fantasy surrounding automation. 05:07 - Is rushing into automation common amongst Chinese manufacturers? - yes, the government and owners are focused on going higher-tech more quickly, but they're walking a tightrope between increasing equipment use and putting too many staff out of work. The usual attitude is that to go up in the value chain processes need to be automated, which is somewhat true, but it's the implementation of automation where things can go wrong if it's rushed into and the pros and cons aren't fully investigated and considered. 07:54 - The benefits & drawbacks of automation in the factory - going through a list, starting with the benefits: Benefits (08:07) Lower costs of equipment in comparison to employing numerous operators over time (labor cost/social insurance/etc) (10:27) Equipment reduces defects over operators (human error) and removes the need for an operator that focuses on rework (11:30) Reducing management overheads and maybe even dispensing with requiring an HR manager to manage multiple staff Drawbacks (12:09) The cost of interest on capital expenditure - quite high in China, around 8-10% (12:35) The costs of specialized staff required to run and maintain the equipment (14:02) Cost of getting the machinery to work properly (setup/time/needing operators to work during this) (15:44) Maintenance - a large driver of costs (parts, downtime, training skilled staff, etc) and really important for highly automated factories (listen to more about preventive maintenance here) (20:36) Automation can reduce a factory's flexibility - manual labor allows a factory to be flexible and provide high mix/low volume work, but automation reduces this flexibility and leans more toward low mix/high volume work. Your higher MOQs may remove the ability to take smaller orders which can return more profit. (22:08) Lead times could be reduced by equipment, but often it's not the case - in theory, automation means more parts can be made more quickly, but often Chinese manufacturers make a lot of inventory and don't take advantage of it and it doesn't improve lead times. 22:57 - Many manufacturers don't take many of the disadvantages into account - this can mean that the cost of equipment VS operators over, say, 10 years works out at more! Pivoting is easier with a human workforce. 24:31 - What are automation best practices followed by the 'best manufacturers?' - Toyota's approach is to automate or remove DDD (dull, dangerous, and dirty) operations without focusing on ROI, as staff safety is more important. 25:59 - The wrong way to implement automation - rushing into heavy automation will cause trouble mainly due to your staff struggling to be skilled and familiar enough to handle the maintenance effectively. This can cause downtime, scrap, and reduced equipment lifetimes so is a serious problem. Before implementing full automation, you should try... 26:32 - Re-engineering human operations - Before implementing automation, the