The Basics of Quality Management for Buyers
China Manufacturing Decoded - A podcast by Sofeast - Fridays
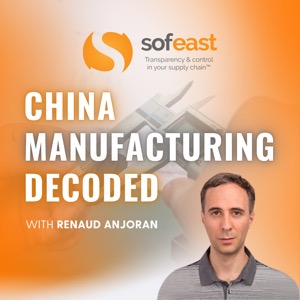
In This Episode... Our CEO Renaud Anjoran (whose background is as a Certified ISO 9001 & 14001 lead auditor, ASQ certified Quality Engineer, and Quality Manager) discusses the Quality Management Process, including its 3 main sections: Planning, QC, and Improvement. This process allows buyers to plan ahead to assure good quality from the start of the project, use real data to pinpoint and eliminate quality issues they're getting from a supplier, and to stop issues from recurring in future by putting in place processes and systems that prevent the issues from reoccurring in future. The takeaway from this episode is a proven QM process which you can use to improve your own quality, and it's based on this graphic which is referred to throughout: Show Notes 00:00 - Summarising the quality management process and its basis in the Juran trilogy, namely the planning, control, and improvement phases. 06:34 - What benefits do implementing such a quality management plan provide to buyers over those that don't pay as much attention to quality management activities? Instead of flying blind, the QM process allows improvement to processes which would otherwise keep throwing up quality issues. Measuring data also allows better control over component suppliers. Overall, poor performance across the supply chain has a negative effect on your business, not necessarily theirs. 11:04 - Best practices for getting started with quality management if you're starting from scratch. As a minimum, document your requirements (what you and your customers will or will not accept) as this allows you to point out if a supplier has done something wrong that deviates from them! Without this, you can see how improving quality may be an issue if a supplier disagrees with your assessment. Based on the requirements, the second key best practice would be to do some QC inspections (including product reliability & compliance) - fundamentally, do the products reach your expectations? 17:56 - Can 'small buyers' affect change? If you're a very small buyer, let's say 0.1% of a factory's output, for example, driving change in your suppliers may not be possible as they will not listen to you. However, if you account for 10, 20, or 30%, for instance, then it's a different story. 18:43 - Do quality recurring quality issues leave small buyers like some FBA sellers in a difficult position? What can you do to protect your business and improve quality? Would it be as drastic as needing to switch to a new, better supplier? Assuming the factory is capable, it may be a design, material, or component issue, so this is worth looking into when you have some quality and defect information. *** Going through each step of the quality management one by one to illustrate the process that buyers can follow in detail. 21:59 - Quality planning Know your customer expectations (a good specification sheet and drawings will be helpful) Set objectives (approving samples is an important step here and boundary samples may be effective if you have a little tolerance between two points) Qualify supplier & sub-suppliers (we refer to this episode on different supplier types) Audit systems and processes, find risks (FMEA), plan accordingly 28:51 - Quality control Product/material inspections (product inspections can be before during and after production, although DUPRO is favorable as there is then time to make changes before all products are finished) Laboratory testing (some samples are sent to labs for reliability/compliance/safety testing, especially if they cannot be done on-site at the manufacturer's facility) 31:00 - Quality improvement Use problems found during auditing or QC to drive improvements Set controls on identified risks (this could be a preventive maintenance plan, for example) Keep updating the quality standard as and when new issues occur, also the risk analysis for when new risks are found, and feed back to the supplier if there are issues with materials or components coming from a certain sub-supplier Extra information you may find helpful Explore this topic in more detail in this blog post over on QualityInspection.org: How Quality Planning Drives QC and Process Improvement Get in touch with us Connect with us on LinkedIn Send us a tweet @sofeast Prefer Facebook? Check us out on FB Contact us via Sofeast's contact page Get even more great content or assistance with your own project Visit our website at Sofeast.com Subscribe to our YouTube channel Subscribe to the podcast There are more episodes to come, so remember to subscribe! You can do so in your favorite podcast apps here: Apple Podcasts Spotify Stitcher Google Podcasts TuneIn Deezer iHeartRADIO