How’s your MEWPs? The skinny on the changes to the Mobile Elevated Work Platform standards with Joe Gagne
MEMIC Safety Experts - A podcast by Peter Koch - Mondays
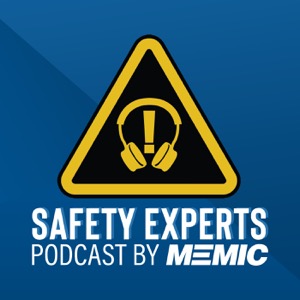
Categories:
Called by many different names: Man lifts, boom lifts, cherry picker, scissor lift, or bucket truck, mobile elevated work platforms are everywhere. They are replacing the traditional ways people work have worked at height. On this episode of the Safety Experts Podcast, I speak with Joe Gagne, Division Safety Trainer at United Rentals to discuss the changes to the Mobile Elevated Work Platform standards. Resources: https://www.forconstructionpros.com/rental/lifting-equipment/article/21104458/accident-data-directs-best-practices-for-mobile-elevating-work-platforms https://www.ishn.com/articles/111059-new-ansi-standard-covers-mewp-design-training-safe-use#:~:text=The%20new%20ANSI%20A92%20standard%20was%20developed%20to%20improve%20safety,officially%20effective%20in%20December%202019. https://constructionexec.com/article/understanding-new-ansi-a92-standard-changes Peter Koch: [00:00:04] Hello, listeners, and welcome to the MEMIC Safety Experts podcast, I'm your host. Peter Koch, called by many different names, could be a man lift, boom lift, cherry picker, scissor lift or bucket truck. Mobile elevated work platforms are everywhere. They are replacing the traditional ways people have worked at height places where in the past you may have seen a ladder or a lift or two of scaffolding or even a man in the bucket of a loader, unfortunately. You now see a MEWP or a mobile elevated work platform. As a matter of fact, just yesterday, as I was leaving a safety conference, there was a scissor lift in the median, with two men standing in it and fixing a messaging sign. They had all of their tools with them, and they were able to easily move the length and the height of the sign. Contrast that with the workplace accident I investigated not too long ago, where a maintenance worker was replacing a lighted sign at the front of the business, where he worked [00:01:00] and fell from the stepladder that he was using. Another example I have a policyholder that's planning to use an electric scissor lift to repair and maintain their indoor climbing wall and some other elevated features in their adventure center. The MEWP that they're looking at had to not only extend to the twenty five foot height necessary to reach the upper holds on the wall, but the data from the Market Insights website shows that the high growth potential for area work platforms is due to rising worker safety concerns across the globe. And no wonder there are much more stable platform for someone to work on than, say, a ladder. And these really aren't the old bucket truck or baskets on a forklift or a loader that we have seen in the past in the construction industry over the last 30 years. The introduction of advanced technologies such as tilt and active load sensors that warn the operator or halt the machine operation when safety guidelines are approached or exceeded, as well as an incredible number of equipment. Configurations and options make these an indispensable [00:02:00] tool for accessing any work area that could be at height. The article for Market Insights goes on to state that one factor that continues to stem the use of MEWPs is the lack of skilled operators and the incidents with these machines that are caused by misuse or lack of proper training. To help us explore more about mobile elevated work platforms. Is Joe Gagne, division safety trainer for United Rentals? Joe, welcome to the podcast. Joe Gagne: [00:02:26] Thank you for having me, Peter. It's a pleasure to be here. Peter Koch: [00:02:28] It's great. And we were talking about this before your voice. I'm jealous right now because it's it sounds great on the microphone. It's going to sound awesome on the podcast. Joe Gagne: [00:02:37] Maybe I'm in the wrong line of business. Peter Koch: [00:02:39] You might. You might be. You give Joe Rogan a run for his money, I guess, right? So you work for United Rentals as a division safety trainer. So tell me about your tell me, tell me a little bit about United Rentals and then tell me about what you do for United Rentals and the scope of the work and how far you travel to do that work. Joe Gagne: [00:02:58] Thanks. Well, [00:03:00] United Rentals is the largest equipment sales service company in the world. We have over 1400 branch locations throughout North America, and we're starting to expand into Europe and Australia right now. And as a division safety trainer, I work with our customers and our employees to ensure that they can operate our equipment safely. A large component of what I do is training and certifying operators, so we bring our folks in and we ensure that they know what the rules and regulations are with the parts and components of the equipment are and what are the best operating practices. So at the end of the day, what's most important is they go home. Peter Koch: [00:03:33] Yeah, absolutely. And we're on the same page. We talked to that as a safety consultant, and I talked to our clients about that all the time. Like the most important thing is your employees go home in more tired than they were when they get in today, if they are going to give you an honest day's work, but they have to go home safely to their family, their loved ones and do other things, not just work. It's the really important part. Joe Gagne: [00:03:54] Absolutely. And that's really where we have to make safety personal. And if we can establish personal [00:04:00] aspect of what they're doing and that's always in the forefront of their mind why they're working, it will keep them safer throughout their workday. Peter Koch: [00:04:06] Yeah, beautiful. And we were talking just before the podcast, some interesting psychological effects that are out there. So we're talking about the Dunning Kruger effect and that interesting notion that people don't know what they don't know until someone comes in and helps them know. And that's your job. Joe Gagne: [00:04:22] Exactly. Unfortunately, there's a lot of misinformation out there in the industry. Folks are told information from somebody that might have been working for their organization for a long time, and they were told from somebody prior to that may not have been fully aware of what the standards, regulations, rules and laws were. So that's where I step in as a subject matter expert for my organization. Peter Koch: [00:04:42] Right on. So let's go down that road because I think it would be interesting to talk about this and let's talk about the myths that you encounter when you get on the job site and you bring a piece of equipment in and or you go to do training with somebody and they are trying to explain to you what they [00:05:00] think the right thing is and. What are some of those myths, so what's the maybe the most popular myth or misunderstanding or misconception that you get when you go to a job site? Joe Gagne: [00:05:09] So the number one myth is I don't need to be certified or trained on this piece of equipment. And the reality is you've always had to be. It's just important to again know what the requirements of training are because different organizations have different standards for training. So we want to make sure that your organization's training is up to the standard that's been published by ANSI, and that's where we ensure that the training that we provide actually exceeds that. Peter Koch: [00:05:33] Yeah, that's awesome. And that's actually my top myth, too. When I go and talk to a client or a policyholder about the, well, fall protection, and inevitably it gets to aerial lifts and we talk about their training. The most frequent training that I find is that, oh yeah, I've got trained. So who did your training? Well, the guy that dropped the piece of equipment off did the training. Well, who did he train? Well, he trained the guy that signed the piece of paper that took the lift in [00:06:00] tow. Well, that's not training like you as the operator have to have training. And it's not just here's the machine. Those are the controls go forth and prosper. It's not that it's more complex than that because they're a very complex machine. Joe Gagne: [00:06:14] Absolutely. And with the new ANSI A ninety two point two for that specifically addresses what constitutes training. It really more clearly defines what training and certification is, and it requires two components. The first is a theory portion of instruction where we go over everything from rules and regulations to parts components to best operating practices fall protection. Once we complete that portion of the instruction, we move on to the practical portion of instruction where each operator is required to get on the machine and demonstrate their ability to operate it competently and safely. When you compile both of those aspects up, then you have a certified operator at the end, provided they can prove that they can complete those skills in the course correctly. Peter Koch: [00:06:56] Yeah, because the beginning part is a more general training, [00:07:00] right? So we'll have specifics to the piece of equipment that you are providing them, but it covers aerial lifts in general. Joe Gagne: [00:07:07] Absolutely. We want to establish a foundation of knowledge that pertains to all aerial lifts, and a lot of that involves, again, the rules and regulations, the stability characteristics of the machine. And just make sure we're clear that there are two different types. There is actual certification training, which the operators require, and then there is specific training for the machine that you're operating and that's called familiarization training. So not only do you need to be certified to operate the machines classification, generally, you need to be familiar with the specific machine that is being operated. Peter Koch: [00:07:38] Good. And I think we're going to get into that a little bit more when we talk about familiarization and what goes into that particular part. But let's get back to the certification piece and you had, you talked about one of those pieces of stability characteristics. What are some other things that might go into that certification, part of the training for an operator? Joe Gagne: [00:07:58] Well, we always want to make sure that the [00:08:00] operator selects the right machine to begin with for their assigned task. Not all the machines are the same. They have different capabilities and characteristics, so it's important to understand the scope of your work first. So you select the most appropriate machine for that task. We often find folks end up on machines that are not best suited for the task they're assigned, and that's really where the domino effect starts. Peter Koch: [00:08:22] Yeah, that's a really good point. It comes up with another myth. I think that we could talk about. When you choose a machine that's not quite suited for the job, you find people either modifying or using the machine in ways that it really wasn't intended. And that's one of those myths. I think that people think that they can make changes to the machine so that it better fits the job. And that's not quite true, is it? Joe Gagne: [00:08:45] You are correct. A lot of folks will try to modify the machine so it suits their need, but you are not permitted to modify the machine in any way, shape or form that isn't approved, designed or engineered by the manufacturer of the machine. Peter Koch: [00:08:57] And good luck with that. Joe Gagne: [00:08:58] Exactly. So that's [00:09:00] where really we want to part with our customers and make sure that they are selecting the most appropriate machine for their task, and we can make recommendations on certain accessories that may aid them and completing their job in a safer manner. Peter Koch: [00:09:10] Yeah, that's perfect. And we were talking earlier too about there is a myriad of accessories that are available. So it's not just the stock machine that you see in the catalog and you have to know like how big it is, how tall it reaches, how stable it's going to be. Will it be able to articulate in the way that you need it? But there's a number of other things that you can get with the rental that will allow you to modify it to be more particular to the task that you need to do. So what are some of the most common accessories that people need? Joe Gagne: [00:09:40] Probably the most popular accessory that we outfit our machines for customers is what we call a glazing kit, and that is simply a shelf unit that is bolted on to the front of the work platform, and it allows the operator to place any type of plated material, whether it be insulated glass, sheetrock or plywood on there, secure it in place and lift it up to a height where it can be mounted or [00:10:00] installed. And again, it's important you're using the manufacturer provided accessory because all of those accessories have capacity limits and you want to obviously make sure you adhere to those limits to make sure you don't tip the machine over. Peter Koch: [00:10:12] Right. So taking a couple of bolts in a drill and adding some framing onto the machine is not the way you want to go. Joe Gagne: [00:10:21] Absolutely not. Some of the things I've seen people construct over the years on these machines would frighten some folks. Oftentimes, we find more modifications occur in the wintertime when the operatives are trying to protect themselves from mother nature and the elements. But really, when you start modifying the machine, you're adding additional weight to it. You may be compromising the guardrail system by drilling holes into it, and you may be creating a kite or parachute or sail in the air to catch the wind and potentially tip the machine over. Peter Koch: [00:10:48] Sure. And you bring up a really great point where any modification done to the machine is not done out of bad intention. It's done out of necessity. There's the individual doing the job is looking at the job and thinking, [00:11:00] Hey, I would be safer. I would be more comfortable if I could have this or do that. And so they're going to try to make it the way they want it. But what I'm hearing from you is a better way to look at that is not once the machines on the ground at the job site to make those changes, but is to do it early on when you're having the conversation with the sales guy from the rental company to figure out what exactly do you need? And there's a particular term for that, I think within the standard correct. Joe Gagne: [00:11:30] There it is. It's called safe use planning. Peter Koch: [00:11:31] Right, I couldn't remember that. So I'm glad you did. Joe Gagne: [00:11:33] And one of the new regulations that was just published or standards from ANSI specifically addresses safe use planning and that falls under ANSI. A ninety two point two two. And really, what you want to do is get a complete scope of what the task is and identify hazards and come up with a risk assessment for those hazards and make sure you select the right machine and do some forethought into what tasks are going to be performed, how they're going to be performed and [00:12:00] what accessories we may be able to put on the machine for you when you do rent one so that you can work safer and within the manufacturer's guidelines. Peter Koch: [00:12:07] Yeah. And I think that's another myth that you've run into is that when people get a particular piece of equipment, they figure that they can use it anywhere on the job site. And I think that it's a misunderstanding because the operator might not have been the person that received the training about the capacity of the machine and how it's supposed to be used. So you find scissor lifts that are designed to be used on flat, hard terrain, outside on rough terrain, and then we wonder why it feels unstable or falls over. Joe Gagne: [00:12:39] Right and one of the nice things is they've actually are now requiring what we call supervisor training, where it eliminates the practice component of the training curriculum. But anybody that supervises or selects or picks out a machine for use on a project needs to be trained, so they need to know what type of equipment is available. They have to do the risk assessment to ensure the work environment [00:13:00] is going to be safe for their folks. So it's really important that those people that are selecting calling in the rentals are aware of all the various different types of machines that are available, so they select the most appropriate one. Peter Koch: [00:13:11] So does the standard. Does the standard require supervisor training now? Joe Gagne: [00:13:17] It does. Peter Koch: [00:13:18] So has that been a change from the previous standard and the update for the new standard? Joe Gagne: [00:13:24] It has been. So that's something we've trying to communicate to our customers that anybody involved with the process of selection, use of the MEWP needs to be trained to the regulation. So oftentimes we find the folks that are responsible for calling in and picking out a machine for rental or reserving one for rental may not know anything, if at all, about the machine and what their capabilities and characteristics are. So it's important to convey that information to them, and they have a full understanding of the scope of work that is to be performed so they can select the most appropriate machine for that task. Peter Koch: [00:13:59] Does [00:14:00] the standard provide tools? Because I think in a lot of places, the person that may be doing the ordering of the machine is not the guy that really has the best idea of what the worksite is going to look like. He might be the parts guy he might be just he might be there to order and reconciliation for the for the company. So are there tools whereby the supervisor can put all the required information together in a form and then get that to the guy who's doing the ordering so he can order the right machine? Joe Gagne: [00:14:33] Absolutely. And that's really where our outside sales representatives for our organization step in and they can provide that type of subject matter expertise and make suggestions based on the findings after the risk assessment that has been conducted for the job site. Peter Koch: [00:14:46] Cool and go back to. So does the, does the standard have a sample risk assessment in there or is it something that the company would need to come up with on their own? Joe Gagne: [00:14:56] It does provide a guidance and outline for what things should be looked for and what [00:15:00] type of hazards should be added? And mitigated. Peter Koch: [00:15:03] That's cool. And I think that's it's a good suggestion, and we'll refer to that later on in the podcast, too, but managers, supervisors, companies who are going to be utilizing these MEWPS need to get access to the standard. They need to know what's in the standard so that they can figure out what they need to do. And if they don't get access to the standard, then the next best thing, or maybe even the better thing is to contact someone like yourself or their rental company so that they know what's required of them. Joe Gagne: [00:15:33] Absolutely. Sometimes we find standards and regulations can be a little confusing to some if they're not used to reading that type of jargon. So I always recommend to reach out to a subject matter expert so we can clarify any information or questions they may have and make us suggestions. And we can also essentially let those folks know what is expected, what they can do to identify and mitigate certain hazards and circumstances on their job site and come up with a comprehensive plan for them so they can work [00:16:00] as safe as they possibly can. Peter Koch: [00:16:01] Perfect. What other new changes are in the standard? So we talked about the supervisor training, we talked about the familiarization training. We talked about the certification. There's been some changes in those. What other changes are in the standard that our listeners need to know about. Joe Gagne: [00:16:17] So probably one of the more impactful one falls under ANSI A ninety two point two two, which is the safe use standard, and that requires that there be a MEWP rescue plan documented by an organization. And on that rescue plan, you have to have two processes or procedures outlined. The first being what process or procedure will be followed immediately following a fall arrest from a work platform. The other process of procedure that needs to be clearly defined and outlined is what will be done in the event you have somebody stranded in an elevated position on a platform. The time to figure out what you're going to do in those scenarios are not when they're happening. You want to have a plan in place and minimize the amount of time that the person [00:17:00] is either suspended because of suspension trauma or the person being stranded in the elevated position. Peter Koch: [00:17:07] Yeah, right on. And there are many organizations out there that don't have those two pieces in place, and they will rely on the user's manual that comes with the piece of machinery to guide them into what the procedures are. And that's not the time you don't want to be rifling through the book when the guy's either dangling off the side of the MEWP or is stuck in the basket, or worse yet, is stuck in the basket and has just been stung by a bee. And he's allergic and you've got to get him down. What do we do? That's not the plan, Joe Gagne: [00:17:39] And the standard clearly states that all folks involved with the operation of the MEWP, whether it's the supervisor, the operator or the designated ground person, have to be familiar with that rescue plan. Again, you want to rescue them in a timely fashion, so the time to figure out what you're going to do is not when those circumstances are happening. Peter Koch: [00:17:59] Right? We'll get [00:18:00] back to rescue in a second because it's one of something that's near and dear to my heart. And I find that in Maine and all across New England, we insure people that are geographically isolated in their work. So you can't always rely on your local fire department to show up to help you, and you might be working by yourself, which is not where we want to go so near and dear to my heart. We'll talk a little bit about rescue in a second, but I want to get back to a term that you just used that designated ground person. So the guys that I saw in the scissor lift working on the sign the other day, there is nobody else around. It was just those guys. The only other guy that was around was the traffic flagger who was directing traffic. And he's not the designated ground guy. Joe Gagne: [00:18:42] He probably was not. Peter Koch: [00:18:44] So tell me a little bit about the designated ground guy responsibilities and what they need to be trained to do. Joe Gagne: [00:18:49] Now you're required to have a designated ground person within visual proximity of the machine at all time during its use and operation. And that's to ensure if something does happen, that that person can come over and render [00:19:00] aid so that ground person is required to be certified as well as familiar with the machine that's being operated. So in the event there is something wrong, they can come right over, provide aid as necessary, Peter Koch: [00:19:11] Right on really important part. And I don't I think it's probably something that a lot of companies aren't thinking about, like if they do seek or reach out to someone for training, they're going to put the worker who is going to be in the basket through the training, but they're not going to put the laborer who is going to be the designated ground guy typically through the training, because for whatever reason, typically it's a cost thing. We've talked about that, that productivity safety rub, there's always friction between Joe Gagne: [00:19:40] Always competing interests. Peter Koch: [00:19:40] You got it. Totally. So aside from saying, hey, it's part of the requirement and yeah, the designated ground person will be able to rescue them. How do you encourage the business owners or the supervisors to get those designated ground guys into the training? Joe Gagne: [00:19:56] Well, first we start by educating them, letting them know what the standards [00:20:00] are and what is expected of them. And again, trying to convey the importance of safety and how impactful it is to their organization, not only from a cost perspective, but from a personnel perspective as well. All it takes is one injury and that could throw the whole project off schedule. One of your key employees are sidelined. So prevention is key. Coming up with that safe work plan and eliminating the likelihood or potential of an accident occurring. So by doing a comprehensive, safe risk assessment. Likely you'll mitigate or eliminate any possibility of anything going wrong. Peter Koch: [00:20:36] Perfect, now and that designated ground person, not the same type of requirement that you would have for, say, permit required confined space like that guy, the attendant his only job is to watch the hole and be in communication so that can that designate a ground person, have other duties like to be the laborer to move supplies and material up to the guys that are in the basket? [00:21:00] Joe Gagne: [00:21:00] Absolutely. They don't necessarily need to be staring at the operator like in a trench situation. They could be doing other tasks, but it's important they stay within visual proximity of the machine while it's in use and operation, and they can act as the designated ground person for multiple machines on a job site as long as they're staying within visual proximity. There may be an event where the operator somehow becomes medically disabled and is unable to communicate his need. So it's important that that designated ground person always have his eyes on the platform to make sure the operator is safe and doing what he needs to do up there. Peter Koch: [00:21:31] Right on. And if there are multiple platforms in that scenario, the designated ground person would need to have familiarization training in each of those machines Correct? Joe Gagne: [00:21:43] Correct. And the nice thing about the regulation here in the United States, comparatively to say Canada is operators are allowed to familiarize themselves with the machine by using the manuals, whereas that's not the case in Canada. So every machine. One of the most integral parts [00:22:00] of that machine is the manufacturer's operating manual. It's a required item and it's going to be located in the black weather resistant storage compartment inside the work platform. I like to call it, your mom. I call it your mom. Because if you take the first letter of each one of the words manufacturer's operating manual, put those three first letters together. It spells mom. So I always tell folks when you're a little kid and say, Dad was at work and you had a question, who would you go ask? You would always go ask your mom and your mom was always riding with you on a machine. So if you have any questions about what an icon means, what a switch does, or what a process or procedure requires of you, you just ask your mom. Peter Koch: [00:22:37] That's perfect. I love it. Can I steal that? Because I might very well use that the next time I go to a policyholder Joe Gagne: [00:22:41] Absolutely and I have to give credit to my colleague, Suzette, who is the division safety trainer in our southern New England area. I actually stole that from her. Peter Koch: [00:22:51] Perfect. All right. Well, kudos to Suzette, because that's a pretty awesome acronym to use, and it's a great way to remember and to also you think about it, I go to a lot of job sites [00:23:00] where they're not renting the piece of equipment. They've owned it for years and mom's not present anymore. Joe Gagne: [00:23:06] That's generally where I find the most deficiencies on equipment is customer owned equipment. And again, it really comes down to lack of knowledge. They don't know what the inspection requirements are. They don't know what is required equipment on the machine. And they generally sometimes fall into disrepair because as long as it's working and getting the platform up to the height, they need to perform their job or task at, then everything's groovy for them. But the reality is, there are some very specific requirements for inspection and maintenance on these machines, and it's important to keep those inspections up to date because things do come out of calibration. Things do wear down. Things do get stressed. So by implementing a proper inspection program and following the intervals of inspection that the standards require, it really cuts down on the amount of maintenance, wear and tear on the machine. And it lessens the amount of downtime you may have on that machine on your job site. All it takes is [00:24:00] one machine to go down, and again, it can throw totally throw off the entire schedule of your project. So by having a robust inspection and maintenance program on your machine, that will eliminate a lot of those problems before they even occur. Peter Koch: [00:24:13] That's great. So what happens if you don't have the manual in there, which is going to give you the operation parameters, it's going to give you capacities, it's going to give you the inspection parameters around that. How do you go about getting another one? I know if one and this would never happen if I got one from United or really any of the other companies that reputable companies that are renting equipment out there, it's not going to come without a manual. But if I own a piece of equipment and I don't have it anymore, who do I reach out to how do I get one? Joe Gagne: [00:24:42] Well, you're more than happy to reach out to any United Rentals local branch office and just request one will be happy to provide you with one at no cost. That's part of us partnering with our customers and other people that are users of these machines to ensure they can work on them safely. Another resources you can actually go right to each one of the machines manufacturer's website, and usually they're going [00:25:00] to have a document library on the website for training manuals, maintenance manuals and generally you can download the specific manual for your machine if you don't have one. Peter Koch: [00:25:09] Yeah, perfect. And I think that's a good point. So reach out to the rental company, but also go back to the manufacturer and see if you can find it there. And it's a critical piece of equipment to have on board with the piece of machinery. So as a business owner or a superintendent of a larger company, you need to make sure that those are present because it gives the user the operator. An integral tool, and I know you provide a really robust training when you come on board, but in reality, what do you expect that operator to remember from the training that you give them? Like how what's the percentage that you expect them to take away and then be able to remember if you came back in a month, what would they what would they have retained? Joe Gagne: [00:25:51] The adult learner? So I do recertification all the time as well and people that I've worked with three, four or [00:26:00] five years ago. And I find that oftentimes if they're not using that information on a daily basis or very often they often compartmentalize that information and they don't access it very often, so it doesn't come right up to their memory. So I always encourage our folks to always read the operations chapter, which is generally the second chapter and the manual, and go over all the various nuances and unique things for that specific machine. I like to joke around with my trainees, and I tell them next time they're headed to the porta potty, grab the manual and it gives them some light reading to do while they're busy, Peter Koch: [00:26:32] Right, there you go. Perfect. That's a great piece because it's right and I do the same thing. I'm sure you would do the same thing with a task that you maybe had training on before or, you know, could be anything from chainsaw operation to hiring a rescue for myself. Like when I get into the rescue season, when I'm doing high angle rescue with my ski areas for the maintenance groups, I've got to spend some time going back through and re remembering operations, [00:27:00] sequences, procedures, how everything functions and works so that I know what I'm doing when I get into the when I get onto the job site. So same thing is going to happen. If it's your construction season and you've been laid off for the winter or you've been transferred to plowing for a while and you're coming back in, it's spring and you're starting to gear up for construction. I mean, your job is to be in that lift. Great suggestion. Find some. Find some quality time with your manual. Joe Gagne: [00:27:27] Quality, quiet time with your manual, wherever that may be. Peter Koch: [00:27:30] Yes, find some quality time with your mom, right? Joe Gagne: [00:27:32] Exactly. Spend some time with your mom. Peter Koch: [00:27:35] Perfect. We should have done this on Mother's Day would have been perfect. So let's get back to the standard a little bit more and talk about some of the other changes that the standard has driven. Maybe. Is there anything that the standard has required about the machine itself? Joe Gagne: [00:27:53] Sure. So that is specifically addressed in ANSI A ninety two point two zero, which evolves around the design requirements of [00:28:00] the machines and the safety features that have to be incorporated into the machines by the manufacturers. Probably the most impactful one we've seen come out of this latest batch of standards is the act of load sensing requirement in platforms where there is sensors mounted on the substructure that the platform was mounted to, and it is constantly and consistently monitoring and evaluating the amount of weight in the platform. And at any point that those sensors detect that it is over its designated weight, it's going to lock out or prevent future or further movement towards greater danger. It will still allow relief functions to be performed, though, because there may be an instance where something heavy falls on the platform. The operator has no way to get it out, but he still needs to be able to get himself safely down to the ground. So it's still allows those relief functions to put the machine back into its most stable configuration. Peter Koch: [00:28:44] So with those with the active load sensors that are on there, they're there to tell you when you are approaching or have exceeded or it won't let you exceed, but you're approaching the limits of that piece of equipment. You don't want to ever get to that scenario, right? [00:29:00] So this comes back to the safe work planning that you have to do ahead of time and making sure that the piece of equipment is going to have the capacity that you need. And when I talk about capacity, it's not just weight. I mean, they'll sense other things as well. So besides the amount of load that's in the basket, what are some of the other things that those sensors are going to take a look at and then provide some feedback to the operator? Joe Gagne: [00:29:25] So a lot of the newer machines have a safety system called the EMS, and that stands for the envelope management system. And depending on the machine, it will allow the platform to be positioned at a certain point within the elevation arc and depending on how much weight or capacity is in that platform, is going to determine how much that platform is allowed to go into the area where it's safe to use prior to these new regulations. It would be up to the user to select the mode or operational envelope the machine could be in based on their assessment of the weight and capacity. Now [00:30:00] the sensors essentially determine it for you. The machines are getting smarter every day to keep you safer every day, and that's a really nice thing to see because we do find most accidents that occur on these machines are generally caused by operator error, and the operator doesn't understand the theories behind stability on the machines. So that's something we really like to focus on in training is to ensure they understand those theories of physics to ensure they don't put them in a situation where it could result in devastating outcomes. Peter Koch: [00:30:32] Yeah, for sure, I don't I don't believe people see, especially, say, an articulated boom lift in the same way that you would see a crane. So when you think about a crane and how much it can lift is going to be based on how big the stick is and how far the stick is away from its center. So it's the same thing with a man lift when you get a boom lift and you're extending farther out from the center. There's a lot that goes into understanding that, so it's good to know that there are some [00:31:00] computers and mechanics in there to help us figure it out. But you never want to rely solely on the computer to make sure you're safe, so you've got to understand what load you're going to have. So when it goes into figuring out what capacity of lift you need, what are some what some of the information that you might need to give the rental person so that they can help you choose a lift that would be configured appropriately? Joe Gagne: [00:31:25] So the first thing we always ask if a customer calls and makes a reservation for a piece of equipment is how high exactly do you need to work? We need to make sure we provide a machine that will get them to that height. We also take into account the horizontal reach capability of the machine. Just because a machine will reach a certain height at maximum platform extension does not mean it's going to have that same extension horizontally. So it's important to understand where you're going to set the machine in relation to the work task to ensure you have the appropriate amount of horizontal reach for the angle that the boom is going to be at. Peter Koch: [00:31:57] Let's take a quick break at MEMIC, [00:32:00] while we strive to help our policyholders prevent workplace injuries, we also understand that they're going to happen. No workplace is immune and when the injury does happen, a solid injury management program must be in place, including reporting and a return to work program. Statistics show that returning an injured worker to work in a temporary modified duty capacity instead of keeping them out of work until there are 100 percent, will reduce both the length and the cost of the claim, as well as increased the likelihood of a positive outcome for the worker and the employer. Did you know that MEMIC has created a seven step process for developing a return to work plan, as well as a matrix to rate your current plan against what our team has found to be the gold standard in return to work? Check out our claim, reporting and return to work resources atMEMIC.com/employers. Now, let's get back to today's episode. Peter Koch: [00:33:01] Right [00:33:00] on, so just because it's a 30 foot boom lift doesn't mean that you're always going to get 30 feet out of it. Joe Gagne: [00:33:07] Correct if you're at a lower boom angle, you're likely only to get 70 to 80 percent of the maximum vertical reach in horizontal reach. Peter Koch: [00:33:15] Yeah. And then the terrain itself will have limiting factors for the piece of equipment as well, right? Joe Gagne: [00:33:21] Absolutely. You've got to make sure the area that you're going to base the chassis of the machine on is firm level and will in fact support the weight of that machine. So you have to take that into account. Often job sites are rough disturb type of terrain, and they may have slopes or grades on them. So it's important to do that preplanning ahead of time. So you make sure you have an asset on site that will actually allow you to complete the tasks that are assigned. Peter Koch: [00:33:43] Yeah, because an all-terrain man lift might be a little misnomer. It's not truly all terrain. There are some limitations. Joe Gagne: [00:33:50] There are certainly limitations. They do have four wheel drive, but I tell people they're not swamp buggies, so you want to make sure that you're going to able to get the machine where you need it. And just because [00:34:00] that machine has four wheel drive capability, it generally only pertains to the machine being in its stowed configuration or transport configuration. Once you actually get the boom up in the air and start scoping out to perform work, you generally don't want to drive and reposition the machine, especially over rougher, disturbed terrain that could cause a lot of what we call a cantilever effect where any type of motion or movement is amplified through the platform all the way up through the boom structure into the platform. And the higher up you are, the further out you are away from the machine, the more cantilever effect you're going to experience. Peter Koch: [00:34:32] It's amazing. How physics can gravity always work? Joe Gagne: [00:34:35] It is, and that's actually one of my favorite aspects of the training that I provide is the theories in the physics behind the stability characteristics. I try to make it as interactive as possible. I get the guys up in the classroom and I have them hold a box or a heavier object close to their chest, and then I'll have them hold that box further out at a 45 degree angle and lock their elbows. And they can see for themselves that the three characteristics [00:35:00] that negatively affect stability height reach and motion they can see with their own eyes and their own body that those three factors do negatively affect stability, so it helps to put things in a context for folks that they can understand. And that's really, in my opinion, what makes a trainer a good trainer? Peter Koch: [00:35:16] Yeah, absolutely. That's a really great point. The more that you can get hands on, the more that they're going to take back with them and they'll remember that activity well, more than they remember the PowerPoint slide that you might have spent 30 minutes on trying to make it look really nice. Joe Gagne: [00:35:30] Absolutely. I try not to use any PowerPoints or audio visual aids in my training. I think we've all probably sat through training before where we had to concentrate really hard not to fall asleep because the subject matter actually wasn't very exciting or the instructor themselves wasn't very engaging. So I really try to make my training's fun interactive and get the guys laughing. And the way I look at it is if they're having fun and they're learning at the same time, that's a recipe for success. Peter Koch: [00:35:57] Yeah, absolutely. We're right on the same page with it. Can I ask you a personal [00:36:00] question about how you got into training? So what got you interested in doing training? Joe Gagne: [00:36:05] Well, actually, it all started off. I come from a construction family. My dad owns a construction company in Windham. And I was very fortunate in the regard that he allowed me to operate a lot of his really big, heavy equipment at a very young age. I owe it really all to my father. He was always the type of dad that showed me how to do things rather than did things for me, and I really found that that was instrumental in leading me to do what I do now. I've always been very technically orientated. I like to pay attention to details, so I like to master tasks. So combining that type of guidance from my father throughout my life and the exposure I was fortunate enough to have around his construction equipment, I'm able to do what I do now. Peter Koch: [00:36:51] Now that's fantastic. It's great to have a mentor in your life like that, whether it's your dad or it could be a teacher, or maybe even a supervisor or someplace [00:37:00] that was able to give you opportunity to learn like that. And then you can see it's paid off in spades for you. Joe Gagne: [00:37:08] It has my parents love to tell the story about whenever there was a snowstorm growing up. I grew up here in the Lakes region, Sebago Lakes Region, and I would always look forward to snow events because I would actually go and ride with my dad and go plowing with them. And I would just always be fascinated by the mechanics of the equipment that was being used and operated, and I would just study things and commit to memory what he was doing, why he was doing it, and how different factors and things affected what he was doing. So I've always really enjoyed understanding at a deep level how things operate. Peter Koch: [00:37:41] Yeah. And then having the opportunity to be able to transfer that information to someone else. I mean that background that you describe is truly a background of someone who can take that information and then find an outlet with somebody else for it, whether it's learning on your own. And then it really seems like you have a love not only [00:38:00] to learn something new, but to transfer or transmit that information to somebody else. Joe Gagne: [00:38:05] It's one thing to become a subject matter expert on something. It's another thing to become a subject matter expert and then be able to convey and communicate that information to other people. So it's understandable, digestible and committed to memory. Peter Koch: [00:38:18] Yeah, interesting. You know, you talk about what makes the most impact on someone. We're going to get into the fall protection conversation. So you think about how to convince someone that, well, you need rescue right away. Yeah. Yeah, fine. Fine. Bring it up to a bunch of construction guys or a bunch of maintenance guys are like, Yeah, fine, fine. We'll take care of it. It'll not be a problem. Well, the sequence of events that I try to do when we're doing a fall protection rescue training is when you go through the limits and capacities and design and function of the fall protection equipment. And then you have them inspect it and then you have them put it on. Get it, fit appropriately, body check [00:39:00] them and then suspend them. So hook it up to the dorsal d ring. Lift them about six or eight inches off the ground and say, How's it feel now? And so if your rescue was 30 minutes away, how do you think you'll feel in 30 minutes? Guaranteed. The answer is going to be it needs to happen now. Rescue has to happen now. And so all of a sudden, the urgency of kind of like holding the box at 45 degrees with your arms locked really connects them to the physics of what the machine's feeling. The same type of deal. That's what they're going to remember. And that's what makes it real for him. Joe Gagne: [00:39:35] Absolutely. You have to connect either a physical or an emotional response to the information you're trying to convey to the people. So one of the things I like to do when I started training session is I like to start off by doing introductions of all the course participants. I asked them their name and I asked them how much experience they have on each piece of equipment. I also asked them what they like to do outside of work. And that's my way of sneakily asking them why they work safely. [00:40:00] I think we all know if you ask somebody, why do you work safely? They might kind of grin at you and give you a snarky answer. But if you ask them what they like to do outside of work, nine times out of 10, I find people mention their family or loved ones spending time with their children, grandchildren or significant other, or maybe even a pet. And I'm looking for that motivation that they might need if I get down the road with them further in the training session where they might need a little more guidance, or I might need them to channel why they want to do this task correctly. And that's my way of knowing why people work safely. Peter Koch: [00:40:35] Yeah, it's great because it really does help you connect, and some of the stuffs can get kind of dry. And if they're not used to using the procedures that you're presenting to them, like, why do I have to go through all of the checks every single day? I just use the piece of equipment yesterday. Why do I have to go through the basket checks in the ground floor? And why do I have to do all that? Why can't I just check it off? Because I knew it worked before? Well if [00:41:00] you need to go home to deal with your family or your friend or whatever, make it real, and I think that's a good way to help. If you need buy in, it's a really good way to get that. Joe Gagne: [00:41:10] Absolutely you need to establish that personal connection with your course participants. And there are a few times where I've had to say, You know what? I know you may not be being very successful right now, but I really need you to take a few moments to compose yourself and focus on the task at hand. And then I may bring up if I remember from the introductions that morning that he planned on going hunting or fishing with this child this weekend. And I'd say, you know what? It really be horrible if you got hurt or injured and weren't able to take your son or daughter hunting or fishing this weekend, wouldn't it? And then you really see those connections, the light bulb moment go off in their head and they realize why they're truly there that day. And it's to learn to make sure that they walk away from our training with the skills and knowledge to operate these machines safely because it can significantly impact their livelihood. Peter Koch: [00:41:59] Yeah, it's not just [00:42:00] the box to check. It really, truly isn't a box to check. Let's talk about the rescue part. So you described that there's requirements for two scenarios or two types of rescue plans that need to be in place. And one is if the machine itself is no longer operable and then the other is if someone actually falls outside of the machine and what has to happen? So what are some of the requirements around each of those? If I had to put a plan together this week for a piece of equipment specific to my company, what things would need to be in it for each of those plans? Joe Gagne: [00:42:32] So there's generally three solutions. The first solution is self rescue. If the person is stranded in the work platform, they would rely on the auxiliary lowering system to bring the platform down to the ground. If the auxiliary system wasn't working, you would rely on your ground person. Now, if self rescue is not viable, you would next bring in a machine of equal or greater size in the platform stranded at, or if the person is suspended, you would do either a platform to platform transfer [00:43:00] or you would literally place the platform underneath the person that is suspended and literally scoop them out of the air. The third option is technical rescue, and that would be provided by EMS. You would have to call your local fire department. Describe the scenario or circumstance you find yourselves in. I always tell folks, let them know specifically how high the platform is because not all ladder trucks the same size. So you want to make sure that the public safety sends the appropriate asset that is going to be able to solve the problem that you find yourself in. Peter Koch: [00:43:29] For sure. And not all local EMS companies have a ladder truck. You get out in some of the more rural areas and that call for heavy rescue because that's what they're really going to be looking for is going to might come from a neighboring town, which extends the amount of time that the person is going to be suspended and there are significant consequences for someone's health. The longer that they're suspended in that in the harness. So you had mentioned suspension trauma. One of my colleagues was [00:44:00]doing a fall protection training actually at one of his one of his policyholders, and he went around the group and started asking them about their experience with fall protection. And one of the typical questions he always asks is so has anybody taken a fall? And you know, after a while, you see somebody in the background who's kind of nodding his head and said, Can you want to tell us about that? And the description that the guy gave this time was it wasn't a far fall, but he was connected to his dorsal d ring fell and actually took about a six foot freefall until the shock absorber connected with him. And he actually pulled back his T-shirt and he had bruises around his traps and through his collar bones because of the force of just that six foot fall. So it's not just suspension trauma. There's other injuries that you can sustain by coming out of the basket or falling off any platform truly. Joe Gagne: [00:44:54] Absolutely. And that's really where it's important to understand the different types of lanyards that are available for fall protection. [00:45:00] There are two different types of lanyards. There's fall arrest that stops a fall that's in progress of what you just described. You're going to fall the length of the lanyard before it begins to catch you. The other and more preferable and safer lanyard style is what we call a self retractable lanyard, which falls under fall restraint that prevents a fall from occurring. So if you slip, trip or lose traction on the platform as soon as your body accelerates, there's a centrifugal break that locks the lanyard in place, and that's going to prevent you from actually falling. So I highly recommend the use of fall restraint, self retractable saddle lanyards over fall arrest lanyards all day, everyday. Peter Koch: [00:45:35] No great, and let's talk a little bit about that piece as well. So if I'm going to connect my fall restraint in my MEWP, where am I going to connect that to? Joe Gagne: [00:45:49] You always want to connect to one of the manufacturer provided designated anchor points. You can't just connect your lanyard to any old guardrail or connection point on the machine. Every single designated anchor point is designed and engineered [00:46:00] to support the. All of a falling person and actually more than a falling person, if you do not connect to the right point, it's not going to do its job the way it's designed to do. Peter Koch: [00:46:09] So are those points designed to where are they located? Are they typically located, you know, waist or chest high? Or are they located on the floor? Joe Gagne: [00:46:18] On most boom lifts, they are generally located at the mid rail and intersection of the vertical stanchion on scissor lifts, depending on the brand and model. Sometimes they may be lower down near the intersections of the toe board and the vertical stanchion. It all depends on the machine. Peter Koch: [00:46:32] Perfect. And in that from a standard standpoint, there's a requirement to have fall prevention or fall protection in a boom lift. How about in a scissor lift? Is there a requirement by the standard to have fall protection harness and lanyard within the scissors lift? Joe Gagne: [00:46:50] There is no standard that requires that in the operation of a scissor lift, although I do highly encourage everybody to always wear fall protection in a scissor lift, specifically [00:47:00] using a safe, retractable style lanyard. Oftentimes, we find that machines tip because the operator goes over the railing, and if he's wearing a fall arrest lanyard, the lateral side force applied to the top of the railing from the lanyard going over the top of it can be enough to pull the machine down on top of somebody. So I highly encourage the use of fall protection using a self retractable style lanyard on a scissor lift at all times, Peter Koch: [00:47:23] Because that's going to help you stay inside the basket, which is the goal because your true fall protection in either is your primary fall protection is going to be your guardrails to begin with Joe Gagne: [00:47:33] Correct. There's two types of fall protection. There's fall protection that's built into the machine itself, which is the guard rail system, and there's self worn fall protection. So it's important to understand the differences between both of those and make sure you use both to your advantage. Peter Koch: [00:47:46] Yeah, capabilities and limitations, for sure. And that's one of the questions that comes up often. And actually, that was witnessed by myself while looking at a couple of guys in that scissors lift. So you could see they had fall protection. [00:48:00] They were wearing a harness, they were wearing a lanyard. But you can see where the lanyard was connected to and they actually had it tied back to itself around the upright corner stanchion of the guardrail. So not at the floor, but it was in the middle. So if they had fallen, the connection point would have slid up into the basically a foot below the top rail and then it would have gone over. So he would have been fairly. That would have been a pretty sizable fall for that scissor lift to have to withstand, Joe Gagne: [00:48:29] Yeah, the safest place always to be on that machine is within the confines of the guardrail system. It's your primary means of fall protection. Peter Koch: [00:48:36] Yeah, 10-4. And so that's one of the things to familiarize yourself with when you get in where your connection points, because I almost guarantee it. I didn't look, I couldn't see it from there, but I would imagine that there were some manufacturers designed and installed fall protection points within that machine. Joe Gagne: [00:48:51] There always is, and they're generally going to be located with a decal letting them know that it is an improved attachment point. You're required to have all decals [00:49:00] that are provided by the manufacturer when the machine is manufactured to be present on the machine. And oftentimes we find as machines, age decals, some bleach or they get peeled off or they fade. So it's always important to ensure that all safety decals on the machine are visible and legible. Peter Koch: [00:49:16] Yeah, it goes back to your conversation about inspections and having a robust maintenance program, because if I can inspect it all the time and I'm recognizing that, hey, some of these stickers or these decals need to be replaced, not quite illegible yet, but they're getting close. You can get them ordered, you can have them in a month. And then when it comes time for annual maintenance or monthly maintenance, they can be replaced. Joe Gagne: [00:49:41] Absolutely. If you do own your own equipment, you can call any United Rentals branch throughout North America. Let them know what make and model machine you have, and we can order up the decals required for that machine. Peter Koch: [00:49:53] Cool. Very cool. So we're getting towards the end of the podcast here, so I got a couple of questions for you. But [00:50:00] before I jump to those questions. Anything else that we need to talk about that we haven't discussed so far that you want our listeners to know about the standards or about the MEWPs themselves. That would be a key point that they could take away. Joe Gagne: [00:50:14] Well, the biggest thing is that now with the new standard, they've broken these machines down into different types based on their classifications and capabilities. So it's important that they're trained specifically on the type in group that the machine falls within. It's not generalized across the entire board, so you want to make sure that your training is going to comply with the standard and regulation and that you're being trained on the type and group of machine that you'll actually be operating great. Peter Koch: [00:50:42] And that goes back to the safe use planning of, you know, making sure that you have all the information and you're going to go back to your rental person, your rental company, give them that information, answer the questions forthright so that they can not only get you into the right piece of equipment, but then provide you the [00:51:00] training that. Necessary for you to become certified and familiar with the equipment. Joe Gagne: [00:51:04] Absolutely. Most folks use self-propelled boom lifts that you can operate and control from the platform. The other type of machine that's pretty popular in the marketplace is the towable type of boom, and those fall under a different group and type. So therefore you need specific training for that type and group. Just because you've been trained on a self-propelled boom lift does not mean that you're certified to operate a towable boom. Peter Koch: [00:51:28] So you had a towable boom and you see those often, especially in the small contractors and painters love those, especially so the towable boom lift. You've got a self-propelled boom lift. What's another class or type of boom if that's out there? Joe Gagne: [00:51:42] The other class is the scissor lift, which falls under Class 3A, and that allows the platform to elevate directly over the circumference of the chassis. So it's again important that you have training that is specific to the type of machine you're using. Peter Koch: [00:51:56] Perfect. Awesome. And again, there's a lot to this. I'm [00:52:00] sure that if you have an industrious group of people at your company and they're really familiar with the standards, they can go through the user's manual, they can create a training program, but it might just be a better use of time, effort and money to reach out to someone like yourself or your company to have them come out and do training for you so that you're taking care of that and then you can come back and do recertification or re familiarization training with them. Joe Gagne: [00:52:32] Absolutely. A Lot of times customers will want to designate somebody within their organization as their trainer and send them to our train the trainer program. It's important to make sure that the person that you do designate for that role, somebody that has a lot of experience on the machine and they are a subject matter expert. I caution organizations from just sending. A certain guy that they might feel might be the best person. And that's because if they're not training or providing that information on a daily basis and staying up to date [00:53:00] on what the current standards are with the best operating practices are and what the new rules and regulations may be, they may not be providing the highest level of training that's available in the marketplace. So that's where it's really important to reach out to somebody that is a subject matter expert on these matters so that they can provide you with the highest level of training that's available. Peter Koch: [00:53:19] Yeah, and it's not just being a subject matter expert about the piece of equipment, and you talked about it before in your interest of training and how you got to be the trainer that you are. Normally, when you get in a company, you get the position of training someone. You're really good at your job, which doesn't mean you're really good at training people. And it really needs to be the relationship of subject matter experts and good trainer needs to be, well, merged in that particular person so that you can assure that the people are coming out of that self training, or that the self-driven training from your company is as functional and as good as it can be. Because at the end of the day, like [00:54:00] you said earlier on, the vast majority of incidents that occur with the MEWPs come from operator error and lots of times it comes because the person's not as familiar as they should be with the piece of machinery or they've missed the piece of the training. So I can't state it enough that having a good trainer and that trainer understanding everything about the piece of equipment being that subject matter expert, it's a key thing. Truly key thing. Joe Gagne: [00:54:33] Absolutely, and I consider myself a constant learner. I am always trying to learn more about these machines. I rely on our technicians a lot for information because they are working on them day in and day out. So oftentimes I'll find a few minutes and go into one of the service technicians in our organization's bay and just kind of pick their brain a little bit and ask them different things. And the wealth of information that they have is incredible. So I consider myself a constant learner. I'm always trying to [00:55:00] gain new information or to come up with different ways to be able to communicate that information to my group of trainees so that they can digest it, understand it and apply it to their circumstance or scenario. Peter Koch: [00:55:11] That's pretty cool. So that kind of transitions to my one of my final questions. So this is a I think it's an interesting question. I had asked me once before when I was working for the ski industry in a particular area. So if cost and technology were not an issue and you have the opportunity to design something yourself, what would it be like? What kind of man lift would you design? No, like talking to the technicians and seeing how they're used all over the place. Like what would be the thing that you would design? Joe Gagne: [00:55:44] Oh, wow, that's a great question. I think a lot of the things that I would incorporate into these machines generally would not be feasible because of the use in nature. Peter Koch: [00:55:52] Ok, Joe Gagne: [00:55:52] That the machines are used for. I would love if there was a laser sight on a platform so [00:56:00] that the operator could appropriately line themselves up and establish trajectory on the boom before they scope out to the work surface. Another thing that I've kind of just thrown around my head, but I know it's not feasible as an airbag system. So if the machine begins to tip, airbags would deploy around the work platform to protect the operator. But again, those are likely unfeasible given the nature and use of this type of equipment in construction environments. But there's some things that I've thought about and I'm like, How can I make these machines safer? So maybe one day I'll come up with a great idea, patent it and become a millionaire. Peter Koch: [00:56:35] Yeah, you never know. I mean, those are two great ideas right away. Just like I didn't. I wasn't even thinking about the basket. I was thinking about airbags just around the base of the machine that that blows up and keeps the machine from tipping over there. So I hadn't even thought of the laser sight, but what a great idea to be able to line up where you're going to go. That's a phenomenal idea. Joe Gagne: [00:56:54] We oftentimes folks get themselves in the most trouble when they move or reposition the platform while they're scoped out to their work surface. [00:57:00] Any type of movement, the higher up and the further out you are, it creates a large amount of sway, swing and bounce. So I try to impress upon my course participants that it's imperative that you line yourself up correctly and make any changes to your trajectory sooner than later. You don't want to be making big movements while you're scoped away from the machine, because that's where that cantilever effect comes in and can really cause some problems. The last thing you want is to smash through a window you might have just mounted or replaced for your customer. Peter Koch: [00:57:28] I was just talking to a client of mine that had a contractor that just did that. They were about seven stories up and they were the contractor had come in. They were painting the side of the building and they put the corner of the man left of the boom lift through a window. So yeah, on movement, right? So it wasn't because it was stationary. The guy was trying to reposition and moved made a larger move. And it came smashing back through the window. Joe Gagne: [00:57:53] Exactly, and that's really one of the things I like to focus on during the practical portion of the training that I provide [00:58:00] is the correct positioning procedures. Oftentimes we find people just assume they can scope out and then boom themselves up. And next thing you know, they're swinging around and swaying six or eight feet as soon as they let go of that controller. So there's methods in this processes that I like to teach and share with my folks. So that doesn't happen. Peter Koch: [00:58:19] Yeah. And so it brings up a great point. You know, it's not just the certification training, but it truly is the familiarization training and even more than that, being a competent operator in their understanding, the limitations and the capacities of that machine because they all go into your plan, how I'm going to get from point A to point B, where am I going to move? How is it going to function? Can I get there? What do I need to do? So great points. Joe Gagne: [00:58:42] Absolutely. That's really where the whole safe work planning is so integral. You want to evaluate whatever your task is and you want to think through the contingencies that could occur. You're always going to be better off solving or coming up with a solution to your issue. If you've already [00:59:00] thought through the various scenarios that could present itself, given your circumstance. Peter Koch: [00:59:03] It's always easier to do it and design than retrofit, right? So I Joe Gagne: [00:59:06] Always have a Plan B, C and sometimes even a Plan D for everything I do. Peter Koch: [00:59:10] A man of like mind with me, for sure. Hey, so one last question for you till we get to the end of the podcast here. So what's one thing that you know now about training people that you wish you knew when you started out? Joe Gagne: [00:59:23] So one thing that I wish I knew when I first started was. You can only give somebody so much information in a training session and expect them to commit it to memory. So I've really refined and sharpen my pencil on the information and the training that I communicate to my folks to hit on the high points. The things that are most impactful to them. If you provide somebody with too much information in a short amount of time, they don't have the ability to compartmentalize that information and then pull it back up when needed. So I really focused on certain key things in my curriculum that I hope my folks will remember and [01:00:00] key things that are going to make the most impact on them working safely and getting home at the end of the workday. Peter Koch: [01:00:06] That's an awesome point, and I think it's a really great point for any trainer out there to remember, especially if you're just starting out because you are the subject matter expert. You've got all this knowledge floating in your head, you've got all these great resources and you get an hour or two hours or three hours and you came to this information over years and years of having hands on and learning and understanding, like you said, being a constant learner. And now you're trying to impart that years and years of information in just a short period of time. And you know, the mind will only absorb what the buck can withstand. That's the idea. And the brain will only absorb so much information. So being able to compartmentalize it and sharpen the pencil, like you said, is a great it's a great suggestion and thought for new trainers. Joe Gagne: [01:00:53] One of the other strategies that I've implemented in my curriculum is I try to establish habits, one specifically involving the worksite [01:01:00] hazard assessment, where any time you step on to a new worksite or a new environment that you'll be working in. You always want to be looking for certain types of hazards. So throughout my training, I have them do that exercise several times because I'm trying to get them to develop and form a habit. So something that they're going to do subconsciously without having to think about it. So every time they step on that job site, they're looking for those five specific types of hazards. Peter Koch: [01:01:26] Cool. That's great. Establishing and especially establishing habits, especially when you have a skill that you're trying to impart and when you start thinking about operating a man lift, there's a skill involved. So there has to be a habit in understanding your work environment needs to be something that you just do out of habit. Great suggestion again for that. So we're getting to the end of the podcast here. And the final question truly, the final question this time is so where can our listeners find more about MEWPs and then more about [01:02:00] United Rentals? Joe Gagne: [01:02:01] Well, folks can find more about United Rentals by going right to our website www.UnitedRentals.com, and if they're looking for a specific training resources, there is a menu on there where you can select training. But if you want to go directly to our training website, it's UnitedRentals.com/training. And if they're looking to schedule or book any type of training for their folks, all they would need to do is call their local United Rentals branch, request that and they will put you in touch with folks like myself. Peter Koch: [01:02:29] Perfect. That's awesome. And if I'm looking for just information beyond that and I'm not quite ready yet to call the rental company, where do I find more information about mobile elevated work platforms? Joe Gagne: [01:02:41] Another great resource online is IPAF.org. IPAF is an organization that stands for international powered access federation, and there are a group of stakeholders in the industry. There's folks from my organization that sit on their board of directors, as well as representatives from the manufacturers of these equipment. [01:03:00] And they're really the trade group that is really trying to push safety and establish best practices and come up with training curriculums that in the end. Turn regular folks into great equipment operators. Peter Koch: [01:03:16] That's awesome, great resource. I was just checking that out the other day to prepare for the podcast, and there are a ton of great resources on that website. So I think between that website and then reaching out to you guys, there's not a whole lot else that you would need to become that good equipment operator for a mobile elevator work platform, Joe Gagne: [01:03:35] Just have to seek out the information Peter Koch: [01:03:37] Right on. So thanks again for joining us today. I really appreciate you being here and sharing your expertise with us, Joe. Joe Gagne: [01:03:42] Thank you for having me. It was a pleasure. Peter Koch: [01:03:44] Right on and to all of our listeners out there. Thanks for joining us. We have been speaking about mobile elevated work platforms with Joe Gagne, division safety trainer for United Rentals. If you have any questions about mobile elevated work platforms or would like to hear more about a particular [01:04:00] topic on our podcast. Email me at [email protected]. Also, check out our show notes at MEMIC.com/podcast, where you can find additional resources around maps and our entire podcast archive. And while you're there, sign up for our safety net blog so you never miss any of our articles or safety news updates, and if you haven't done so already, I'd appreciate it if you took a minute or two to review us on Spotify, iTunes or whichever podcast service that you found us on. And if you've already done that, thank you because it really helps us spread the word. Please consider sharing this show with a business associate friend or a family member who you think will get something out of it. And as always, thank you for the continued support and until next time, this is Peter Koch reminding you that listening to the MEMIC Safety Experts podcast is good, but using what you learned here is even better.