Testing our Safety Resolve
MEMIC Safety Experts - A podcast by Peter Koch - Mondays
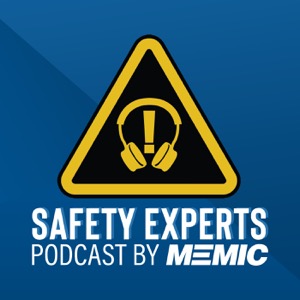
Categories:
The word resolution implies a steadfast intent to succeed or change something. While this may be true for the New Year, the word is better used to describe the movement or change between things. On this episode of the MEMIC Safety Experts Podcast, I discuss how a resolution should be a living thing, especially when it comes to safety. Peter Koch: [00:00:04] Welcome to the MEMIC Safety Experts podcast, I'm your host, Peter Koch, manager of digital technology for Lost Control and a safety management consultant here at MEMIC. I'm recording this episode as we transition into two thousand twenty two and wow, what a whirlwind it's been. One of those eddies of that whirlwind has really been this podcast. It's hard to believe that the podcast has just celebrated its two year anniversary in November of 2021. It's not something that we could do without you listening, and because of you, we've resolved to keep it going. And you know, that got me thinking about the word resolution. And at this time of year, more than any other, it's a word that gets tossed around a lot at one that I expect some of us have been less than successful with over the years, myself included. In general, that word has come to represent that a decision has been made around an intention like the New Year's resolution. Of [00:01:00] course, like I firmly resolved to change or I firmly resolved to do or not to do whatever. However, that tends to be a fairly narrow definition. The word resolution has more uses in depth than what we have come to connected with this time of year. So get beyond the New Year's resolution, and the word connotes something opposite of an unwavering decision to do something. Consider, like in music theory and composition, the term resolution means to progress a chord from dissonance to consonants, or from something that sounds unstable or creates tension to a note that is more stable or creates a sense of release. This clip that you're going to hear next is Howard Shore's Score The Hobbit and is a good example of movement from the tension of dissonance and the release of resolution. Peter Koch: [00:03:11] In [00:03:00] this case, this is a part of the theme from The Trolls from The Hobbit, and that their bad guy status has really made clear, by the use of a semitone dissonance at the end of the musical phrase and I'm sure you heard it, and if you were paying attention to it, you might actually get that emotional sense of movement, of tension, of something that's going to happen and that doesn't resolve. And then finally, it does resolve. Another definition of the word resolution is used when analyzing a complex notion into simpler ones or solving. Again, this has a feeling of movement. I'm going from a bucket of stuff, lots of complex things together, and I'm trying to break it apart into its component parts. So going from one state to another, like when separating a chemical compound [00:04:00] into its constituent parts through process of distillation, chromatography or even extraction, another use for the word resolution is for the subsidence of a pathological state, such as inflammation. So like, it goes away, it's resolved. It's change. It's gone from a painful area to something that's no longer painful. Last, the use of the term resolution is used when making something more distinguishable or to make individual parts clear, such as in optical resolution. And we hear that all the time in photography, especially digital photography, or when you're trying to pick out an LCD projector for your presentations or a television, right, you're looking at the number of pixels per inch or the resolution of the particular device that you're trying to choose. Peter Koch: [00:04:48] The higher the resolution, the better clarity that there's going to be for the detail that you'll have. These alternate uses of the word resolution describe much more than a decision to [00:05:00] or not to do something, and more often than not, resolution describes the movement of something or a change. I see the word resolution being one that describes the dynamic relationship between one thing and another. It refers to the release of the tension between the state of what something is and what you want it to become. In my opinion, this is how we should see our resolutions. Not a concrete decision, right? I'm going to stick to this and nothing is going to make me waver because I know in the past that has not been a successful place for me to start. Whenever I do that, I tend to fly off the handle sometimes or things will change. Circumstances in my life will change. Circumstances around the resolution will change and all of a sudden, I'm no longer firmly resolved the way I was before. So it's not a concrete decision, but it should be the journey between where you are and what you want to become and the path that you're going to take. That's the resolution. How do I know [00:06:00] where I am and where am I going to go? Peter Koch: [00:06:02] So with that in mind, and as it is the season for New Year's resolutions, I think it's a good time to reflect on what safety resolutions we can make for the coming year. And the way I see workplace safety is that it's a journey and all of the things that we do to help us move or our company move in one direction or another. That's the resolution. And because safety has everything to do about the human being and how they interact with the workspace, that journey is not always easy, nor is it exponential. However, in order to move forward, we do need to recognize the reality of where we are and where we can go. So consider again the example of music. If you've ever heard dissonant chords or the musical phrase never resolved, you would be in constant tension, but kind of like a frog in the pot. You wouldn't realize that you're in constant tension, but there would be all the effects of that constant tension. You would have, you [00:07:00] know, maybe an increased heart rate or increased anxiety, or you would get really focused on what's going on in front of you instead of seeing what's happening around you because you have nothing to compare it to. You wouldn't realize that you could change your circumstances or even want to change it because, well, some people like living in tension and an overall living in tension sometimes isn't a bad thing, but we want to make sure that we're able to recognize the tension that we're in and maybe that there's a better place for us to go. Because while some tension is good, constant tension fighting against the desire or the need to produce and the looming potential for injury or death is not good. So first, recognize where you are. Do you know what your injury rate is? Well, how does it compare to your injury across the nation? So, for example, it's an interesting story. I was at a workplace discussing with the leadership what I had found to be an inordinate number of injuries for that particular [00:08:00] company. And while we were talking, I was really surprised to receive a true lackluster or a resigned response from the team. And when I had asked them how they felt they were doing, their response was that they felt they were doing the best they could. And of course, most of the injuries were the fault of the workers, not their particular issue. So I left it in. We continued our discussion and it was clear as we went on that they believed that they were a top tier business when it came to what they produce and the quality of the product that they had, and that they had a team of workers that were critical to the mission of the business and the success that they were enjoying. Well, I asked the safety questions again in a different way. I asked if they felt that they were in the top ranking nationwide for their company and how do they think they compared to their peers in safety? The response was that other businesses like theirs had just as many injuries and they were right in line with everyone [00:09:00] else. Peter Koch: [00:09:01] Well, this was in February, so I asked them what their OSHA injury rate was or their DART rate. So they pulled it from their OSHA 300 log and what they found was a five point three. So their injury rate was about a five point three. So not huge. I've certainly worked with other industries that had a much greater OSHA overall injury rate. However, five point three is still a significant number of people when we pull the BLS data for their NAICS code. That rate was two point five, so two point five nationally for the NAICS code, where theirs was specifically a five point three for their company, more than twice the national rate. So when we dropped that bomb, you would imagine that there might have been a pause and there was. And then right afterwards there was a rash of excuses and all the normal ones. Well, it's the employee's piece. They don't listen, we have to we really have to push productivity in order to maintain our [00:10:00] income levels and our business levels. But as we kept going through those excuses, they gradually realized that they were not in the place that they should have been or really could have been. And it was only then that we started to discuss the inconsistencies in the safety, culture and what was said or written down in policy and the reality of what was happening on the ground level where employees were actually doing the work. Peter Koch: [00:10:28] The leadership's resolution was to start work at identifying what was causing the disconnect and make changes that would positively affect the safety culture. We didn't discuss what incident rate they should resolve to get to, but we did make a point to evaluate the incident rate every year to see if the results of what they were changing affected the injuries at the company. And sure enough, in three years they had a safety culture survey result that was more positive and that their injury rate or incident rate had dropped to a three. It [00:11:00] still wasn't below the national rate, but what was much better than where they had started, and they really recognized how they got there and that they still had some room to grow. So what kind of safety resolutions should you be making this year? Well, no resolution should be made in a vacuum, and I need a little more creativity. So I pulled our team of safety management consultants here at MEMIC to put a wish list together for what resolutions they want their policyholders to make. The first suggestion that was given to me, I think, hits the beginning of movement, from dissonance to consonants or from chaos to order. It asks that a company should identify what to measure and what success would look like. This first resolution comes from Laurette Wright, who works closely with our policyholders in the health care industry. Laurette Wright: [00:11:47] Hi Pete it's Laurette, I would like my policyholders to identify two or three KPIs or leading indicators that measure [00:12:00] safety performance for 2022. Peter Koch: [00:12:04] The next suggestion for a resolution comes from Jason Hebert. Jason works with multiple industries here in Maine and makes a recommendation that, if so implemented, will help normalize the understanding of the importance of safety and help with buy in around the safety procedures and policies that need to be followed for success. Jason Hebert: [00:12:25] If I was able to choose a resolution for my insurance, it would be to implement a learning process for their safety training programs. Learning must be a process versus an event, starting with identifying business needs or knowledge gaps within the workforce. Next, to find the training objectives to address each of these gaps and provide training to educate and reinforce safety expectations. Equally important, and follow up to the training, managers and supervisors need to circle back to ensure that new knowledge is transferred to the job. In my observations, oftentimes training is provided with no [00:13:00] follow up. Learning needs to be a process, not just an event, to be effective. With that, my resolution for twenty twenty two is for each of my policyholders to review the current training programs, identify opportunity to improve effectiveness and improve to ensure that business needs are met. Peter Koch: [00:13:18] Deb Willard Webb, who works with all industries on our ergonomics team, is up next. She has a penchant for connecting the vision of leadership with the insight of the front line staff. Again, she provides a resolution that involves gaining clarity, not just an unbending rule or focus on a number. Deb Willard Web: [00:13:37] I'd love to hear policyholders resolve to include line staff in development of corrective action once they identify root causes for injuries, and to do that with enthusiasm, believing they can identify actions that will make a difference to [00:14:00] recurrence. So I'm not sure how to make that more concise, but that's the gist. Peter Koch: [00:14:05] Al Brown MEMIC's own director of ergonomics, has a suggestion that can have a significant effect on injuries and on employee work capacity. This involves an understanding of your current situation and what your workplace would look like if implemented. Sometimes a change like this one requires you to break down your process and illuminate areas that small changes can be made too, to best facilitate the whole. Al Brown: [00:14:31] My resolution for two thousand and twenty two is that all industries that handle material don't put anything on the ground, they don't have too. Keep it between your knees and shoulders and 35 pounds in between. Peter Koch: [00:14:48] The next suggestion for a resolution comes from Natalie Campaneria and really highlights the role of leadership and safety. Natalie, like most of the safety management consultants here at MEMIC, came [00:15:00] from the industry that she serves, and she has experience with how company leadership can make or break workplace safety. Again, a resolution to move. Natalie Campaneria: [00:15:10] I have a resolution that I would love to have all of our policyholders make, and that is that the leaders make safety part of their priorities when they're walking around. Be a good example. If you see something on the floor, pick it up, reinforce positive behavior related to safety and just let the staff know that you're thinking about their safety, their health, and that you care about them. Peter Koch: [00:15:37] Last for this reflection on what we can do to change safety for the positive. I look back at the challenges that 2021 has dropped into every business across the nation, and this recommendation for a resolution comes from Rob Sylvester, and I think it really hits home. So regardless of whether the challenge is COVID or reduced production or supply chain problems [00:16:00] or the aptly named great resignation, Rob suggestion is at the heart of every resolution that brings a company safety program or process into harmony with its other business goals. Rob Sylvester: [00:16:13] My message to all is lead with compassion and with empathy and always, always be genuine. Take care of your people and they will take care of your clients, your customers, your residents, patients or whomever they work with. You're happy and healthy employees are the key to your company's success and always be present in the moment, especially in your personal life. Here's to a happy and successful 2022. Peter Koch: [00:16:38] Take care of your team and they will take care of your company. No, no, you can't please everyone all the time. But if your resolutions connect the well-being of your team to the results, then you are on the path to long term success. So what's your safety resolution for twenty twenty two? I know most of us have room to grow or [00:17:00] move from a place of tension to a place of order in our company safety programs. So if you have an idea for our resolution or your company has made a safety resolution for 2022, then send them into me via email at [email protected]. We'll do a future episode looking at what different companies have done and maybe even reach out to you to get some more detail. Well, that about wraps up this week's Safety Experts podcast. Thanks a lot for joining us. The MEMIC Safety Experts podcast is written, hosted and produced by me, Peter Koch. I'd like to thank all of those other folks here at MEMIC who have supported this podcast like Rod Stanley, who does a lot of work with coordinating guests, or Kelly Barton on the communications team, which helps with the promotion of the podcast. So if you have any ideas for a safety topic that you would like to hear an expert discuss on the podcast, email me that as well at [email protected]. Also, check out this episode's show notes at [00:18:00]MEMIC.com/podcast, where you can find more safety resources, as well as our entire podcast archive. While you're there, sign up for our safety net blog so you never miss any of our articles or safety news updates, and if you haven't done so already, I'd appreciate it. If you would subscribe to the podcast and then take a minute to review us on Spotify, iTunes or whichever podcast service that you found us on. And if you've already done that, thank you because it really, truly helps us spread the word. Please consider sharing the show with a business associate friend or family member who you think will get something out of it. And as always, thank you for the continued support. Until next time, this is Peter Koch wishing you a great start to the New Year and reminding you that listening to the MEMIC Safety Experts podcast is good, but using what you learned here is even better. Peter Koch: [00:18:55] Before you sign off from the podcast, listen to a little bit about MEMICs loss control services. [00:19:00] Integrating workplace safety into your business is a key part of the long term success for any company. And like most components of success, there is no one size fits all solution. MEMIC is committed to partnering with employers across all industries for workplace safety, and we recognize the key to that partnership is understanding the unique demands of the industries that we insure our safety experts bring experience from the industries that they serve. And this experience provides unique perspective through a critical eye when it comes to understanding the particular exposures and challenges of an industry from construction, retail and manufacturing to hospitality and health care. Our team of experts will work with policyholders to identify opportunities to improve safety. Interested in finding more about MEMIC? Check us out at MEMIC.com or better yet, contact your local independent insurance agent for more information. If you're already a MEMIC insured, [00:20:00] then check out our safety resources at MEMIC.com/WorkplaceSafety and sign up for access to our video lending library, our LMS platform, or our Safety Director Resource Library. Thanks very much for listening.