175. Communication Is Key to Successful Power Projects
The POWER Podcast - A podcast by POWER
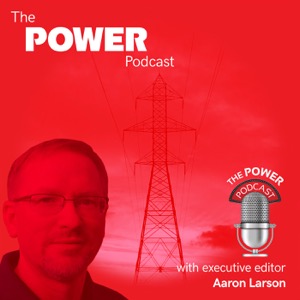
Categories:
Power plant construction and retrofit projects come in all shapes and sizes, but they all generally have at least one thing in common: complexity. There are usually a lot of moving pieces that must be managed. This can include sourcing the right materials and components, getting equipment delivered to the site at the right time, finding qualified contractors, and overseeing handoffs between working groups. Getting a job done on time and on budget is not as easy as some people might think. “It absolutely can be difficult and a lot of things to consider,” Kevin Slepicka, vice president of Sales for Heat Recovery Boilers at Rentech Boiler Systems, said as a guest on The POWER Podcast. “You’ve got to make sure that communication is ongoing between your suppliers and the end user.” Rentech is a leading manufacturer of boiler systems including package boilers, waste heat boilers, and heat recovery steam generators (HRSGs). Rentech’s fabrication facilities are in Abilene, Texas. “We have three shops,” Slepicka explained. “There’s 197,000 square feet of manufacturing space under roof. We’ve got over 100 tons of lift capability with cranes, and we can bring in other cranes for our heavier lifts. Our properties are located on 72 acres, so we have a lot of room for staging equipment, storing equipment, if customers aren’t ready to take delivery at the time the units are done.” Moving large boilers from Texas to sites around the country and other parts of the world can be difficult, which is another reason why good communication is imperative. “Shipping is a major consideration on how the unit is constructed, how much is going to be built in the facility, and how large we can ship. So, it really goes hand in hand with the design of the boiler,” Slepicka said. “It really is important that we work with our logistics people and work with our partner companies that do our transportation for us.” Communication with customers on potential future needs is also important. Slepicka said knowing that a retrofit may be required down the road to account for a new environmental regulation, for example, could allow a boiler system to be designed with space to accommodate changes. This could save a lot of money and headaches in the long run. “That’s where you’ve got to be able to work with the customer—make sure you understand the space available and make sure that the unit’s going to work properly,” he said. Slepicka said Rentech had a customer recently that faced new formaldehyde restrictions and needed its HRSG system modified. “Luckily, we had the space in the unit where that catalyst could be installed in the right location to address the concern they had, so it was a relatively easy retrofit for them to make.” If the prospect had not been considered up front, the cost and complexity could have been much greater.